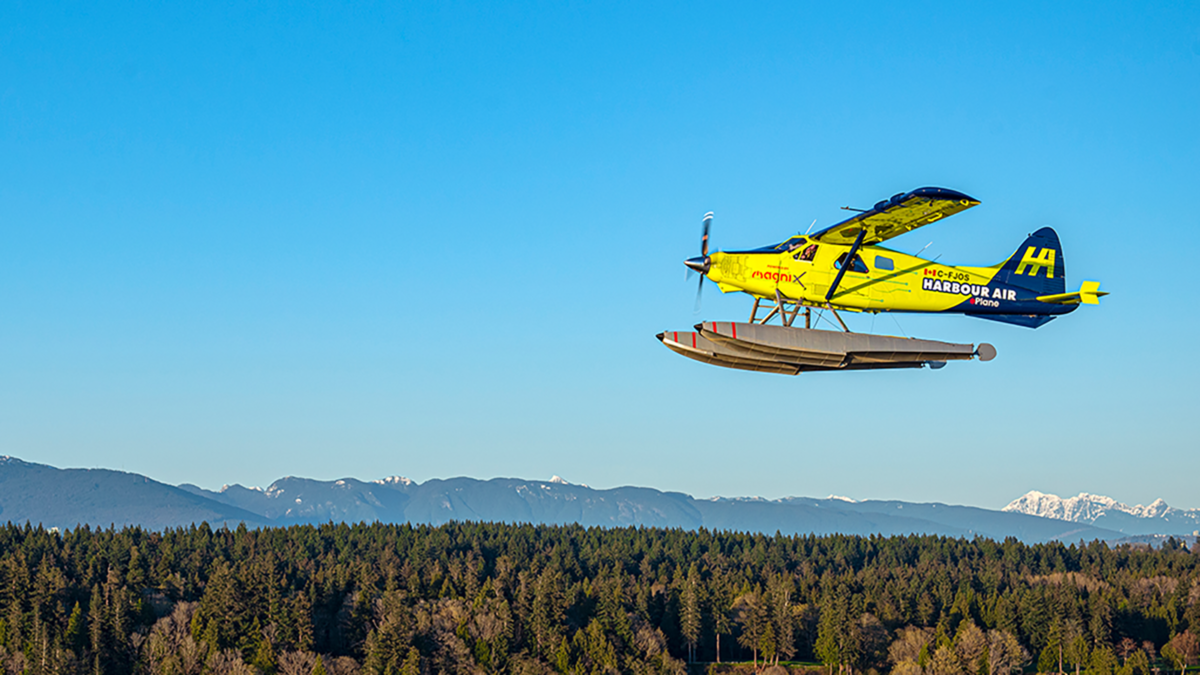
Electrified aircraft ground and flight tests continue progress toward sustainable aviation
Gokcin Cinar and Phil Ansell in Aerospace America
Gokcin Cinar and Phil Ansell in Aerospace America
The excitement around electrified aircraft technologies continued to grow as development and testing programs achieved new milestones.
In February, the National Research Council Canada, or NRC, performed the first flights of its hybrid-electric Cessna 337 Skymaster. Referred to as the Hybrid Electric Aircraft Testbed, or HEAT, this aircraft’s rear turboprop engine was replaced with an equivalent-power electric propulsion system, in this case an electric motor powered by batteries.
In May, Beta Technologies of Vermont completed a 2,200-kilometer flight with its Alia electric vertical takeoff and landing aircraft. The flight lasted eight days, and the aircraft made seven stops along the way to recharge its batteries.
Also in May, Pratt and Whitney Canada announced that H55 of Switzerland would supply the battery for its regional hybrid-electric flight demonstrator, with support from NRC and the Innovative Vehicle Institute for integrating the high-voltage battery system. This follows Pratt and Whitney’s July 2021 announcement of its collaboration with Collins Aerospace and de Havilland Aircraft Canada to retrofit a Dash 8 with hybrid-electric propulsion, with hopes of improving fuel efficiency by 30%.
In June, Tier 1 Engineering of California completed its first flight test of the all-electric Robinson 44 helicopter powered by a magniX electric propulsion unit. The helicopter flew for three minutes over Los Alamitos Army Airfield in California.
The U.S. Department of Energy’s Advanced Research Projects Agency-Energy invested a combined $55 million into three programs to support the development of ultra-efficient electrified propulsion systems. Kicked off in June, the Connecting Aviation by Lighter Electrical Systems, or CABLES, program is focused on low-loss and lightweight electric wires and cables. The other two programs, Range Extenders for Electric Aviation with Low Carbon and High Efficiency, or REEACH, and the Aviation-Class Synergistically Cooled Electric Motors with Integrated Drives, or ASCEND, have been underway for more than a year and completed promising system concepts and component demonstrations. Teams are scheduled to demonstrate technologies in the 2024-2025 time frame.
In July, GE Aviation completed ground tests on its high-power, high-voltage hybrid-electric integrated system at NASA’s Electric Aircraft Testbed facility in Ohio. The ground tests of the motors, generators and power transmitters simulated operations at altitudes up to 45,000 feet. NASA and GE will transition to flight tests as part of NASA’s Electrified Powertrain Flight Demonstration project.
In July, Ampaire’s hybrid-electric EEL demonstrator completed an 1,800-kilometer flight from Mojave, California, to Oshkosh, Wisconsin. Ampaire stated it was the single longest nonstop flight by a hybrid-electric aircraft to date.
In August, seaplane airline Harbour Air of Canada announced that its all-electric ePlane completed its first direct point-to-point test flight. ePlane, a retrofit of a de Havilland Beaver, flew 72 kilometers in 24 minutes on 100% battery power.
Throughout the year, NASA marked several developments in aircraft electrification through its University Leadership Initiative. A team led by Ohio State University developed an advanced modular integrated motor and drive prototype configured with a rated power of 1 megawatts at an operating voltage of 2 kilovolts. The machine was sent to NASA’s Armstrong Test Facility in Ohio for further commissioning and experimental testing in September. Another team through the Center for High-Efficiency Electric Technologies for Aircraft, or CHEETA, led by the University of Illinois at Urbana-Champaign completed the conceptual design of a hydrogen-electric transport aircraft with a cryogenic, superconducting electrical power system and a 2.5-MW superconducting machine design. In September, NASA announced intent to award a second phase of the CHEETA ULI that focuses on prototyping cryogenic machine hardware and superconducting and superconducting power systems, alongside a hydrogen-electric scaled flight demonstrator.
This article was part of Aerospace America’s Year in Review. This annual publication can be found here.