
Structures & Materials
Structural mechanics is the study of the mechanical behavior of solids and structures. Aerospace structures differ from other structures due to their high demands for performance and lightweight. Modern aerospace structures typically require the use of composite materials, advanced multifunctional materials and thin-walled constructions.
To obtain the level of performance required from flight structures, thorough knowledge of material limitations, structural stability, structure health and strength considerations are needed. Current research in the Department emphasizes the characterization of advanced materials, material and structural stability, computational material/structural design, thermo-mechanical and electro-mechanical interactions, structural dynamics, multiscale modeling, multifunctional structures, smart structures, morphing structures, aeroelasticity, structural health management and design optimization. This specialization covers theory, computations, experiments and implementation issues, as well as the study of specific cutting edge aerospace vehicles. In many cases, new software is being developed to address these issues for future air and space vehicle structures.
Structures & Materials FACULTY
Structures & Materials RESEARCH GROUPS
Active Aeroelasticity and Structures Research Laboratory
The search for more efficient and higher performance aircraft comes with a host of exciting new problems to solve! The Active Aeroelasticity and Structures Research Laboratory (A2SRL), founded and directed by Professor Carlos E. S. Cesnik, is a multidisciplinary lab focused on finding novel solutions to the myriad of complex problems related to conventional and unconventional aircraft. A2SRL is defined by its members! A strong collection of students, postdocs and faculty with a diverse set of skills enable cutting edge basic and applied research in multi-physics modeling, analysis, simulation, and experimentation. At A2SRL, we believe in testing our theoretical developments and seeing our ideas put into practice. To support the research conducted in the lab, we have built a wide variety of computational and experimental facilities that allow our members to work on projects ranging from model-order reduction of complex systems, control design for load alleviation, multidisciplinary design of very flexible aircraft, all the way to complete multiphysics hypersonic vehicle modeling & simulation. We also like to conduct flight tests of our own very flexible testing platform, the X-HALE. Our goal has been to identify, develop and pioneer modeling, analysis and design tools that will ultimately enable building the next generation of greener aircraft, advanced air mobility, and high-speed air vehicles!
Adaptive Intelligent Multifunctional Structures (AIMS)
The AIMS Lab at the University of Michigan (Umich) is run by Professor Daniel J. Inman and investigates methods of advancing the field of aerospace engineering through smart materials and morphing structures.
AIMS research is the culmination of the study of controls (through reinforcement learning and adaptive control), fluid dynamics, structural dynamics, and materials science that make up aerospace engineering as a whole. What makes the AIMS Lab unique is that our research embraces many of these fields. Overall, we strive to develop innovative and novel solutions to complex aerospace engineering dilemmas via smart materials and structures but we take a multidisciplinary approach by working at the intersection of simulated and experimental structural dynamics. Ultimately, this applies to a wide variety of research including energy harvesting, structural damping, metastructures, and aircraft morphing. Much of our morphing UAV work is motivated by researching avian flight.
Our lab consists of a 1×1 low speed wind tunnel with PIV system for flow measurements, an altitude chamber for testing in the temperature and pressure of flight up to 100,000 ft and numerous dynamic measurement systems.
Adaptive Materials and Structures Laboratory
The Adaptive Materials and Structures Laboratory, directed by Professor John Shaw, is dedicated to the fundamental research of thermo-mechanical coupled field effects in complex materials, especially shape memory alloys (SMAs) and elastomeric components at elevated temperatures.
The AMS laboratory is equipped with three general purpose testing machines for stiff materials such as metals and composites, soft materials such as elastomers and for impact and cyclic tests. We can also control temperature through environmental chambers through air temperature, thermoelectric devices and a fluid circulator bath.
Thermal analysis equipment, including a differential scanning calorimeter are dynamic mechanical analyzer, is available for accurate thermodynamic materials characterization. It provides heat capacity and latent heat measurements as well as accurate dynamic and static measurement of thermomechanical properties of small, or low force, specimens.
Various optical imaging equipment and infrared imaging equipment are available for full-field deformation and temperature field measurements, respectively. This equipment can accurately measure and post-process temperature fields as temperature color contours. It has been used quite effectively in the past for the thermo-mechanical characterization of shape memory alloys that exhibit stress-induced exothermic (and endothermic) phase transformations.
A custom-built membrane inflation facility is available that can be used to perform experiments on pressurized thin membrane specimens, elastomers or thin film SMAs, at elevated temperature. Through the use of multiple CCD cameras, photogrammetry has been performed to measure to the non-uniform multiaxial strain field on the surface of the membranes.
Aerospace Materials Laboratory
Aerospace Materials Laboratory is directed by Professor Henry Sodano. It is a research laboratory focused on the development and application of active materials. This lab provides a cultivating atmosphere for which research professionals, academia, graduate and undergraduate students can collaborate on the solution to modern technological problems through material systems.
Composite Structures Lab
Professor Anthony Waas is the director of Composite Structures Lab. The research in this lab is dedicated to the development of validated analytical and computational methods to understand how a structure (such as an air-vehicle wing, a fuselage, the load bearing structure of a land-vehicle, the wing of an insect, a wind turbine blade) made of multi-materials responds to external environments.
To achieve this goal, researchers perform a combination of experiments, computational modeling and analysis, and theoretical developments when necessary. Data driven modeling that incorporates physics and machine learning is of current interest. Several faculty colleagues and students from the Aerospace Engineering department and from a variety of other departments at Michigan, and external collaborators from other institutions, government labs, and industry partner with us to achieve the goals of our group.
Multidisciplinary Design Optimization Laboratory
Professor Joaquim R. R. A. Martins founded the Multidisciplinary Design Optimization (MDO) Laboratory research group in 2002. Research in the MDO Lab embraces both the theory and applications perspectives. On the theory side, we develop numerical methods that are applicable to a wide range of problems. Much of our work has focused on the accurate and efficient computation of derivatives to aid gradient-based optimization methods, but derivatives have many other applications. The complex-step method for computing derivatives, for example, has been applied to a wide range of disciplines, including geophysics, biotechnology and statistics. We have written a survey of MDO architectures, and we are constantly looking for opportunities to improve these architectures. We are currently collaborating with NASA in the development of OpenMDAO, a framework to facilitate the application of MDO to real world engineering design problems.
On the applications side, our focus has been on the optimization of aircraft configurations with the objective of minimizing environmental impact. Much of our effort has been in researching methods to enable high-fidelity aerostructural optimization, which optimizes aerodynamic shape and structural sizing simultaneously, leading to the optimal aeroelastic tailoring of wings. This led to the development of the framework for MDO of aircraft configurations with high fidelity (MACH). Using this framework, we have found wing shapes that minimize takeoff weight and fuel burn for a given mission, as well as configurations that minimize the aggregate fuel burn for thousands of missions. We have also considered the optimization of composite laminates and compared optimal metallic wings with composite ones. Another potential of application of aerostructural optimization is in the design of wind turbines.
Multi-Scale Structural Simulations Laboratory
The Multi-Scale Structural Simulations Laboratory (MSSL) is directed by Professor Veera Sundararaghavan. Our interests are in the areas of computational mechanics, multi-scale materials modeling and optimization with emphasis on prediction, and design of properties in aerospace materials. Multi-scale models resolve interactions of material structure and mechanisms at electronic (ab-initio), atomistic (molecular dynamics), micro (mechanics of slip), meso and macro (finite element models) scales. We develop models to address key aerospace issues such as optimization of material properties, computation of property degradation in high temperature environments and design of failure-resistant microstructures.
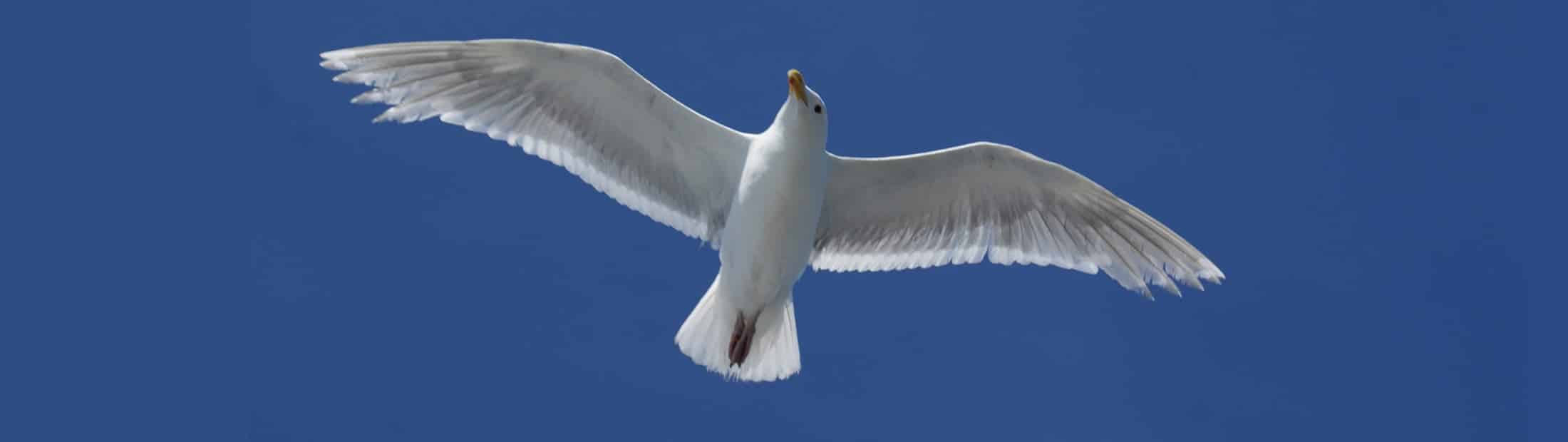
RECENT Structures & Materials NEWS
Selected Research ProjectS
Carlos E. S. Cesnik
- Clarence L. (Kelly) Johnson Professor
- Director of the Active Aeroelasticity and Structures Research Laboratory, Director of the Airbus-University of Michigan Center
- Research interests: Multifunction active aeroelastic structural modeling, analysis and design; structural health management
Peretz P. Friedmann
- François-Xavier Bagnoud Professor
- Director, FXB Center for Rotary and Fixed-Wing Air Vehicle Design
- Research interests: On-Blade Control of helicopter rotor vibration and noise using active flaps, microflaps and active flow control. Aerodynamics and aeromechanics of coaxial rotors. Hypersonic vehicle aeroelasticity and aerothermoelasticity emphasizing the multiphysics nature of the problem. Aerothermoelastic scaling of hypersonic vehicle components
Vibration Reduction in Helicopter Rotors using Active Flow Control
Effectiveness of active flow control to reduce vibrations in helicopter rotors in forward flight using open loop and closed loop flow control was demonstrated for the first time.
Aeromechanics of Coaxial Rotors Using Viscous Vortex Particle Method
Unsteady aerodynamic interactions in coaxial rotors are complex and can be best captured by the VVPM.
Hypersonic Vehicle Aerothermoelasticity and Aerothermoelastic Scaling
The aerothermoelasticity of hypersonic vehicles is a complex multiphysics problem involving coupled fluid-thermal-structural interactions that are computationally demanding and can be effectively modeled, by reduced order models (ROMs). A computational framework to address these problems, is being developed and improved continuously. It can simulate the response of hypersonic vehicle components, as well as aerothemoelastic scaling laws required for their wind tunnel testing.
John A. Shaw
- Professor
- Director of the Adaptive Materials and Structures Laboratory
- Research interests: Active materials, smart structures, material instabilities, thermo-mechanical constitutive modeling.
Active Materials
Experimental and theoretical studies of shape memory alloys, such as NiTi, providing an understanding of the coupling between the mechanical and thermal behavior of the material.
Design, fabrication, and testing of novel cellular forms of SMAs to develop new types of thermal actuators and highly resilient structures.
Active Structures
Design, fabrication, and testing of novel cellular forms of SMAs to develop new types of thermal actuators and highly resilient structures.
Thermo-mechanical Constitutive Modeling
Constitutive modeling at the continuum and atomic lattice scales to capture the complexities of therm-mechanical coupling and material level instabilities in shape memory alloys and elastomeric materials.
High Temperature Degradation of Elastomeric Components
Experimental and theoretical studies of the chemorheological behavior of elastomeric materials at elevated temperatures to develop service life predictions for elastomeric components.
Experimental Mechanics
Development of infrared imaging, custom-built temperature control facilities and photogrammetry techniques to enable constitutive thermomechanical experiments.
Veera Sundararaghavan
- Associate Professor
- Director of the Multi-Scale Structural Simulations Laboratory
- Research interests: Computational mechanics, computational material science, multi-scale modeling, atomistic modeling of materials, computational materials design.
Micro-structure-sensitive design
Multi-scale homogenization and finite element sensitivity analysis techniques are developed to optimize microstructures of aircraft materials so that mechanical properties are enhanced. With this approach, polycrystalline materials with tailored elastic modulus (see figure), yield strength and magnetic hysteresis loss distributions have been developed. Simulations are performed on a 200 processor Beowulf cluster at the Center for Advanced Computing. Mathematical model reduction and statistical learning methods are used to facilitate rapid exploration of the space of material variability and generation of property closures with a goal to optimize properties in aircraft materials.
Multiscale approaches for simulation of composite property degradation
We are interested in multiscaling (continuum-atomistic, finite element homogenization) and coarse graining (multi-body expansion, cluster expansion) techniques for linking simulations at different length scales. Such techniques are used to compute property degradation of composites in high temperature (eg. propulsion, reentry) environments in the presence of oxidation and matrix-fiber interface separation (atomistic phenomena) and bulk transport of gases in the matrix and thermal stress development (continuum phenomena).
Atomistic modeling of deformation and failure
Deformation and failure of structures and interfaces at atomistic length scales are studied. We employ molecular dynamics (MD) and more accurate first-principles simulations (DFT) for modeling phenomena such as grain boundary behavior (see figure), interface sliding and separation. Non-linear constitutive relations that describe complex microscopic processes are subsequently employed in continuum FE simulations. Features such as stress concentrations at the tips of the distributed cracks that cause plastic deformation in the grain interiors are studied using such approaches.
GET INVOLVED
Be a part of research that pushes the boundaries of aerospace engineering.
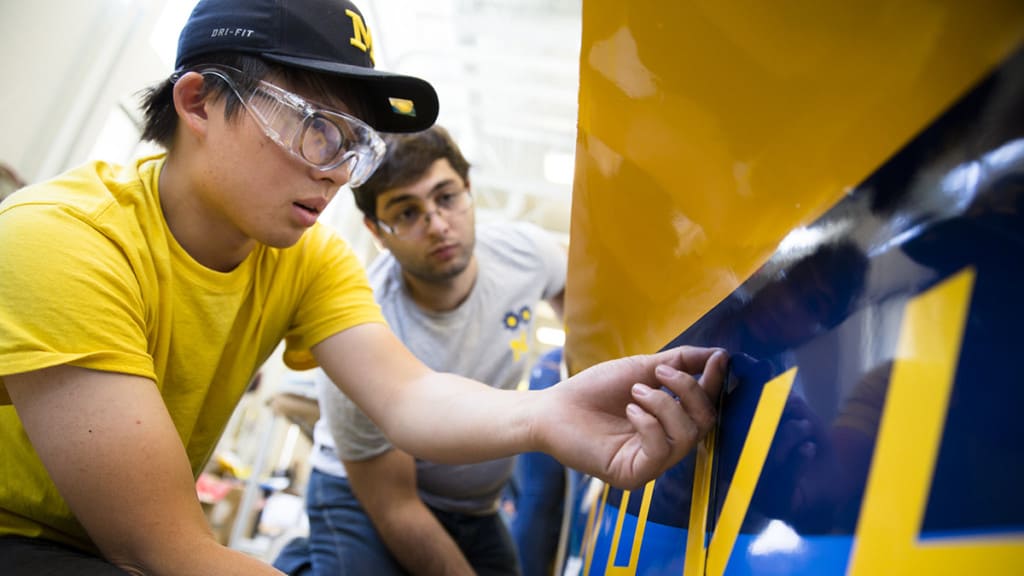